-
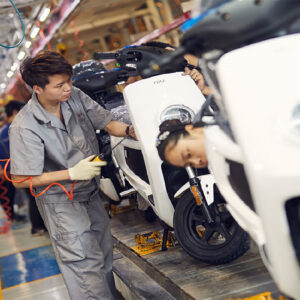
The two-wheeler assembly line mainly includes parts inspection, frame assembly, power system installation, suspension setup, wheel and tire mounting, braking system assembly, electrical system installation, fuel system assembly (for motorcycles), body and cosmetic parts fitting, functional testing, final inspection, and packaging for shipment. These steps ensure a smooth manufacturing process from components to the finished product.
-
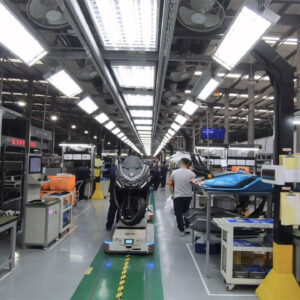
The motorcycle assembly line integrates processes for efficient, high-quality production. It includes frame assembly, engine installation, electrical and fuel system setup, suspension and braking system installation, wheel and tire mounting, bodywork fitting, quality inspection, performance testing, and final adjustments. Finished motorcycles are then packaged and shipped. This line emphasizes detail, flexibility, and quality control, with technological advancements enhancing automation and efficiency.
-
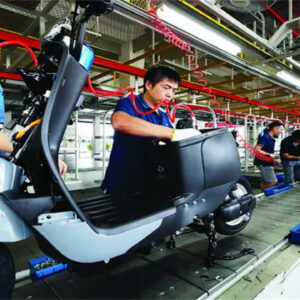
The E-bike assembly line involves frame welding, motor and battery installation, electrical assembly, wheel assembly, braking system setup, accessory fitting, function testing, safety checks, quality inspection, and packaging. This process ensures efficient, safe production of high-quality electric scooters.
-
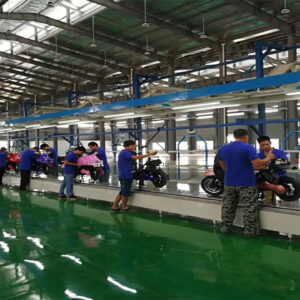
E-bike CKD production lines involve importing fully disassembled parts for local assembly, offering tariff benefits and boosting local manufacturing skills. They create jobs, ensure quality control, and are flexible to adapt to market demands. These lines are cost-effective, environmentally friendly by reducing transportation impacts, and contribute to industrial development in the host country.
-
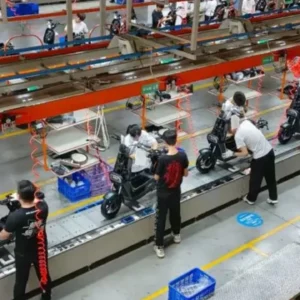
The E-bike CKD/SKD assembly line is used for efficient local assembly of electric bicycles. It involves receiving pre-manufactured parts, conducting quality inspections, and then final or partial assembly according to CKD or SKD kits. This includes electronic system configuration, wheel assembly, suspension and frame integration, braking system installation, overall assembly, performance testing, quality control, and packaging for shipment. This assembly method is flexible and cost-effective, helping to meet local regulations and reduce transportation costs.
-
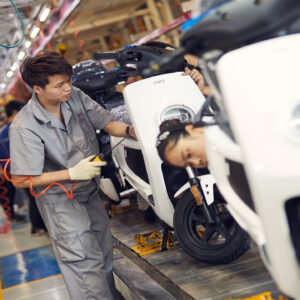
The E-bike SKD assembly line is tailored for semi-knocked down electric bike assembly, focusing on customization, quality control, and safety. It integrates automation systems for efficient production management. The line prioritizes the assembly of key components like batteries and electric control systems, ensuring environmental protection and performance standards are met.
-
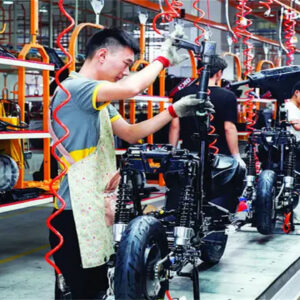
The electric scooter production process includes design and prototyping, material sourcing, cutting and shaping parts, assembling motors and batteries, wiring circuits, frame assembly, quality testing, and packaging for shipping. This ensures efficient, reliable scooters that meet daily commuting needs.
-
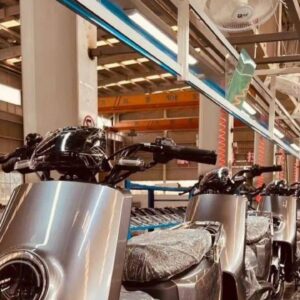
The E-scooter CKD assembly line involves disassembling electric scooters into components for assembly in target markets. This approach reduces costs, adapts to local demands, avoids high tariffs, and supports local production. Key steps include part reception and inspection, sorting and storage, assembly, electronic system setup, performance testing, quality control, final inspection, and packaging for shipment. This flexibility allows quick market response and cost efficiency.
-
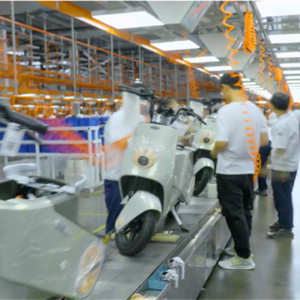
The E-scooter intelligent assembly line features automation for tasks like welding and component assembly, ensuring efficiency and quality. It’s designed with modularity for flexibility across models, incorporates energy-saving and eco-friendly practices, and integrates intelligent systems for real-time monitoring. Safety is paramount, and performance testing is crucial to meet speed, range, and climbing standards.
-
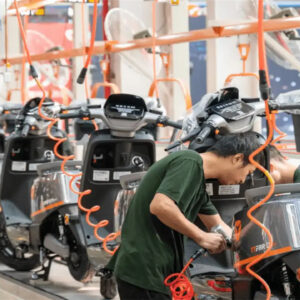
The E-bike assembly line mainly includes preliminary part assembly, motor and battery installation, electronic control system assembly, handlebar and cable wiring, final assembly, performance testing, quality inspection, painting and decoration, packaging and logistics, and data tracking and feedback. These stages ensure a smooth manufacturing process from parts to finished products.
-
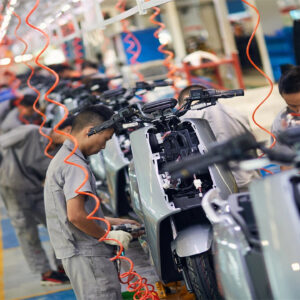
The electric scooter assembly line is designed for efficient assembly, with customization, high load capacity, and flexibility. It integrates automation, is easy to maintain, and prioritizes safety. Adaptable for various models, it’s energy-efficient and ensures continuous production with built-in quality control.
-
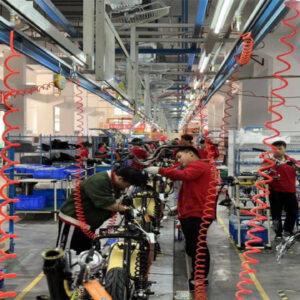
The motorcycle assembly line assembles various parts into complete motorcycles efficiently. It includes stations for frame, engine, electrical system, suspension, and body parts assembly. Quality control is integral, ensuring each motorcycle meets safety and performance standards before leaving the line.
-
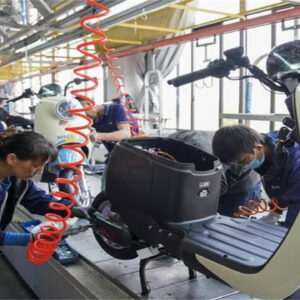
Motorcycle final assembly lines feature automated equipment for precision, modular designs for flexibility, and quality checks to ensure standards. They adapt to various models, comply with environmental regulations, and use information systems for process optimization. Safety is prioritized, and continuous improvements are made for better quality and efficiency, with customization options available.
-
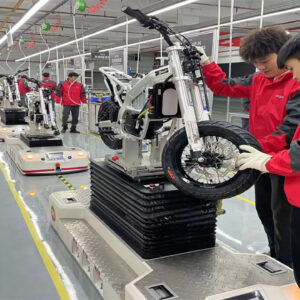
Motorcycle assembly lines have achieved a high level of automation, featuring automated material handling with RGV systems, intelligent quality control through vision recognition and sensors, and data analysis for optimization. They integrate MES for efficient production management and utilize AGV technology for flexible assembly, adapting to market demands and cost pressures.
-
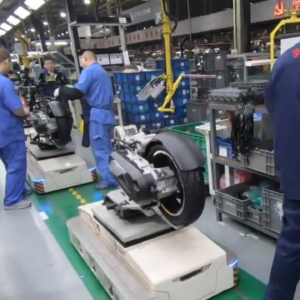
The motorcycle final assembly line includes key components like assembly stations, electric and pneumatic tools, rotating platforms, quality inspection equipment, and automation systems. These ensure efficient assembly and quality control. Daily output varies based on automation, worker skills, process design, equipment reliability, and other factors.
-
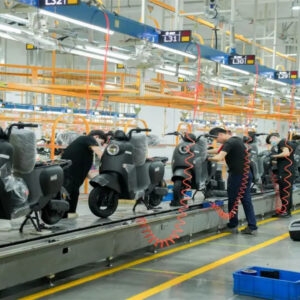
The two-wheeled electric vehicle assembly line involves component inspection, frame assembly, motor and battery installation, electronic control system setup, wheel and tire mounting, suspension assembly, electrical wiring, body and cosmetic part fitting, functional testing, quality inspection, and packaging for shipping. These steps ensure a smooth manufacturing process from parts to the finished product.